The vicious cycle of benchmarking product output with material input (or the Input Output ratio)
- Vaibhav Verma
- Jul 19, 2022
- 2 min read
Updated: May 26, 2023
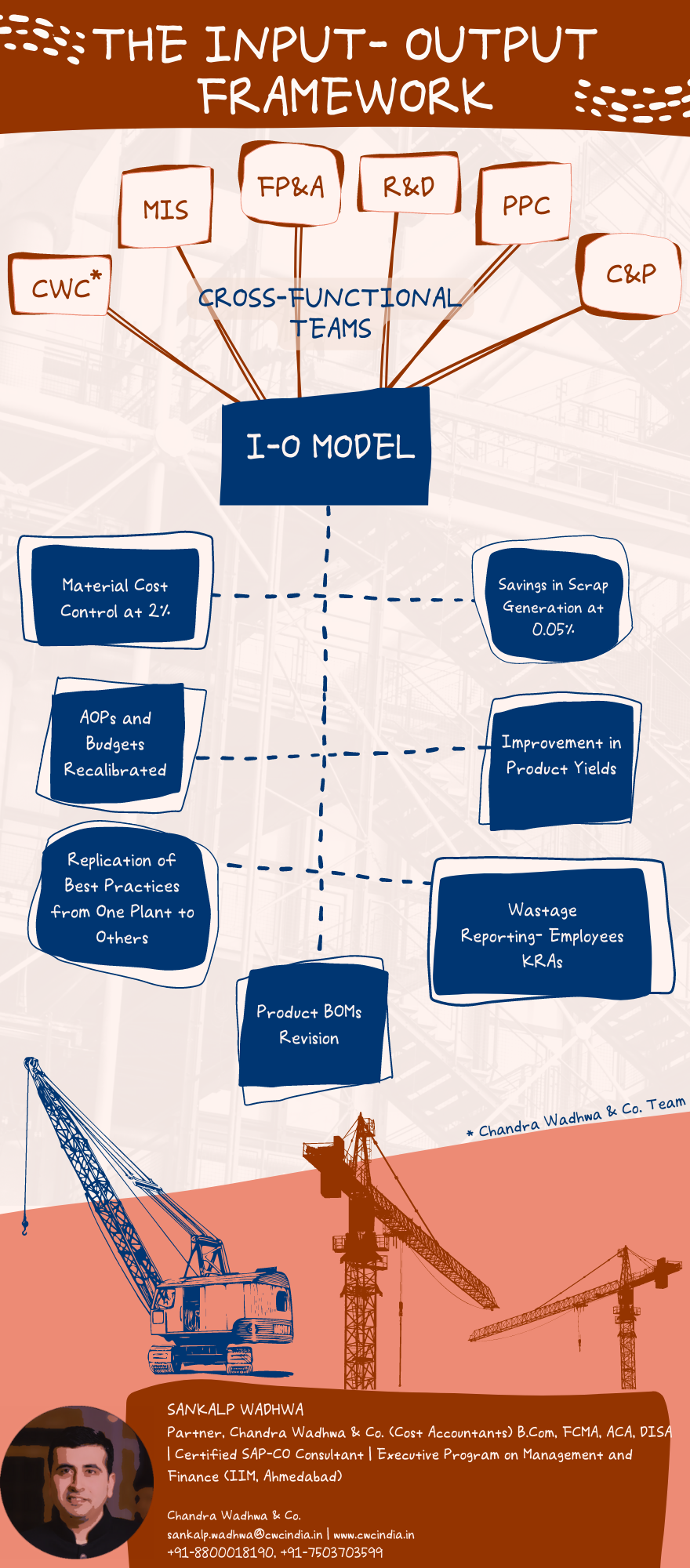

THE INTRODUCTION:
This client is one of the leading building solution providers and pre-engineered steel building manufacturers. Its building products and solutions are available in more than 1,00,000 villages and 600 cities in India and over 35 countries globally.

THE PROBLEM:
The company has six state-of-the-art manufacturing facilities with a PAN India presence catering to the demand of ~1 Million MT of building products. Their problem statement is two-fold:
Understanding the reasons for the divergent production yields and material usage efficiency for different products across different plants.
How to measure and address the above anomalies.

THE SOLUTION:
To develop a framework/ control mechanism that analyses the plant-wise input-output (I-O) ratio [1] and yield efficiency. Accordingly, a cross-functional team was formed, including various departmental heads of the company, as follows:
Management Information System (MIS) and Cost Accounting
Financial, Planning and Analysis (FP&A)
Research and Development (R&D)
Production, Planning and Control (PPC)
Contracts and Procurement (C&P)
After intense brainstorming and coordination between the cross-functional team, a concrete and well-informed methodology was devised to compute plant-wise standard benchmarks in the I-O ratio.
The following was observed in the computed benchmarks:
Every plant contains a different set of standards as their benchmarks.
Within the same manufacturing facility, huge variances exist in the standards on a month-on-month basis.
Varied yield efficiency across plants.
Normal Scrap loss witnessed across all plants was not standard, dependent on the quality and quantity of material mix.
Standard consumption benchmarks were used in designing the I-O framework, along with actual quarterly material consumption figures across all plants. In addition, we took steps to ascertain yield efficiency, i.e. how much yield is produced from actual material consumption compared to standard material consumption.

THE RESULTS:
After rigorous deliberations and continuous collaboration with the cross-functional team of the client for two months, our team at Chandra Wadhwa & Co. implemented a comprehensive and feasible I-O model Refer to Exhibit 1, offering the following key insights to the management:
Successfully control the material costs to the tune of ~2%.
Annual operation plans (AOP) and budgets were re-calibrated based on material usage and yield standards as derived from the implemented I-O model.
Best practices/ processes from one plant were replicated to other plants to minimise variation discerned in the process losses across plants.
Normal standard loss was defined for each plant based on various parameters, including process efficiency, raw material quality, temperature conditions, etc. Variances over and above standard losses were reported to the management and became part of the employees' KRAs (Key Result Areas).
Savings in scrap generation was witnessed to the tune of ~0.5% of total material consumption cost.
Yield losses were computed accurately, leading to redefinition/ revision of product BOMs (Bill of materials) as well as accurate forecasting of scrap generation (process/ product).
Product yields improved significantly across all manufacturing locations Exhibit 1 An extract of Input-Output (I-O) Model.

Exhibit 1 An extract of Input-Output (I-O) Model

FOOTNOTES:
1: ⌃ Input output (I-O) ratio signifies raw material consumption quantity per unit of production output.

FREQUENTLY ASKED QUESTIONS:
What is benchmarking?
Benchmarking is comparing the performance of a company, process, or product against industry standards or best practices to identify areas for improvement and optimise performance.
What is the input-output ratio?
Input-output ratio refers to the relationship between the amount of material inputs and the amount of product output. In manufacturing, a high input-output ratio means that a lot of materials are required to produce a relatively small amount of product. In contrast, a low input-output ratio means fewer materials are needed to make a larger product.
What is the vicious cycle of benchmarking product output with material input?
The vicious cycle of benchmarking product output with material input refers to the tendency of companies to focus solely on increasing product output without regard for the amount of materials required to produce that output. This can lead to a high input-output ratio, which in turn drives up material costs and reduces profitability.
How does benchmarking product output with material input impact a company's performance?
Benchmarking product output with material input can impact a company's performance in several ways:
It can lead to higher material costs and lower profitability due to a high input-output ratio.
It can result in lower product quality due to using cheaper or lower-quality materials.
It can lead to environmental and sustainability issues due to the excessive use of materials and energy.
It can reduce competitiveness in the market due to higher costs and lower quality.
What are some strategies to break the vicious cycle of benchmarking product output with material input?
Some strategies to break the vicious cycle of benchmarking product output with material input include:
Focusing on process optimisation and waste reduction to improve efficiency and reduce material usage.
Implementing a sustainable procurement strategy that emphasises using environmentally friendly and cost-effective materials.
Investing in research and development to improve product design and reduce material usage.
Implementing a circular economy approach that emphasises the reuse and recycling of materials.
Encouraging collaboration and knowledge sharing with suppliers and partners to identify opportunities for cost and material reduction.
CONTACT US
Reach us if you have any concerns regarding cost management accounting issues in your organization.
SANKALP WADHWA
Partner, Chandra Wadhwa & Co. (Cost Accountants) | B.Com, FCMA, ACA, DISA | Certified SAP-CO Consultant | Executive Program on Management and Finance (IIM, Ahmedabad)
Address: 1305 & 1306, Vijaya Building, 17, Barakhamba Road, New Delhi - 110001, India Mail: sankalp.wadhwa@cwcindia.in
Tel: +91-8800018190, +91-7503703599.
Website: www.cwcindia.in
Comments